Surface Treatment Methods for Perforated Metal Panels of Different Materials
Source:www.cn-psp.cnAuthor:河北森驰公司 Last updated:2025-04-15 09:30:50 Browse:
Perforated metal panels are widely used in architecture, industry, and decoration. Surface treatments not only enhance aesthetics but also improve durability, corrosion resistance, and pollution resistance. Depending on the material of the perforated metal panel and the usage environment, various surface treatment methods can be applied, including painting, powder coating, fluorocarbon spraying, galvanizing, electro-polishing, and anodizing.
1. Painting
Painting is commonly used for perforated metal panels made of iron and aluminum. By applying a layer of colored paint, both appearance and basic corrosion resistance are improved. The paint not only changes the color of the metal but also forms a protective film that slows down the impact of environmental factors. This method is generally used indoors or for decorative purposes where high corrosion resistance is not required.
Advantages:
Cost-effective
Wide range of color options, easy customization
Suitable for indoor environments
Disadvantages:
Poor weather resistance; prolonged outdoor exposure may cause fading or peeling
2. Powder Coating
Powder coating (also known as electrostatic powder spraying) is a popular surface treatment method. Using electrostatic technology, powder coating is evenly applied to the metal surface and then cured by heating. Compared to traditional painting, powder coating offers better corrosion resistance and a smoother, more durable finish. It has strong adhesion and effectively resists UV rays, humidity, and chemicals.
Advantages:
Excellent corrosion resistance
Smooth surface and stable color
High production efficiency, suitable for mass production
Disadvantages:
Coating may be less effective on complex-shaped perforated panels
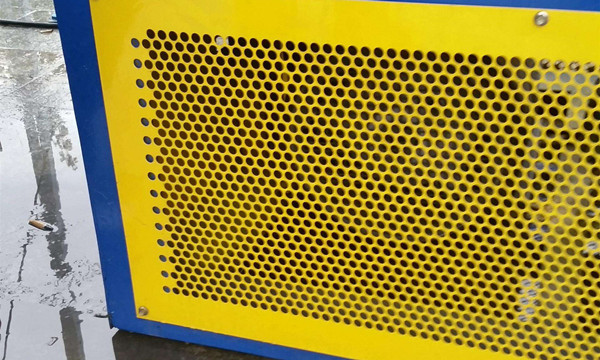
3. Fluorocarbon Spraying
Fluorocarbon spraying is a high-end surface treatment technology mainly used in construction and decorative applications of perforated metal panels, especially in harsh weather environments. Fluorocarbon coatings offer excellent UV resistance, preventing fading, cracking, and other weather-induced damage. Due to its superior weather and pollution resistance, fluorocarbon spraying is often used for external wall decoration and exposed architectural facades.
Advantages:
Superior weather resistance, ideal for outdoor use
Excellent UV, acid rain, and pollution resistance
Long-lasting color retention
Disadvantages:
Higher cost, suitable for premium applications
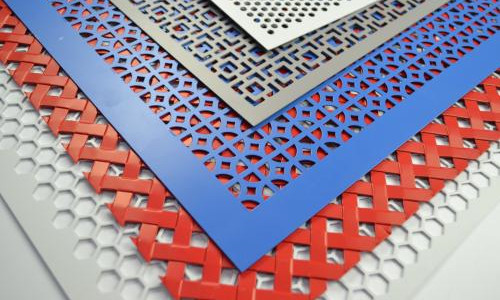
4. Galvanizing
Galvanizing is a common surface treatment for iron perforated metal panels, forming a protective zinc layer through electroplating or hot-dip galvanizing. Hot-dip galvanizing provides a thicker and more durable zinc layer than electroplating, making it especially suitable for humid or acidic environments to effectively enhance corrosion resistance.
Advantages:
Effectively prevents rust and extends service life
Hot-dip galvanizing offers better corrosion resistance
Disadvantages:
Zinc layer thickness may be limited, not ideal for extremely harsh environments

5. Anodizing
Anodizing is a surface treatment primarily for aluminum perforated panels. This electrochemical process forms a protective oxide film on the surface, enhancing corrosion resistance, wear resistance, and heat resistance. Anodized aluminum panels come in a variety of colors and retain a metallic luster, commonly used in architectural decoration, especially in high-end applications such as perforated curtain walls and screens.
Advantages:
Enhanced corrosion and wear resistance
Available in multiple colors, ideal for decorative use
Environmentally friendly and non-polluting
Disadvantages:
Only suitable for aluminum; the process is relatively complex
6. Electro-Polishing
Electro-polishing is mainly used for stainless steel perforated metal panels. It significantly improves surface smoothness and brightness. Through electrochemical reactions, small protrusions on the metal surface are removed, resulting in a smoother, more uniform finish with higher reflectivity. Electro-polished perforated panels offer better anti-pollution performance, are easier to clean, and provide improved corrosion resistance. This method is widely used in high-end decoration, food, and pharmaceutical industries.
Advantages:
Enhanced gloss and smoothness of the metal surface
Strong pollution resistance, easy to clean
Improved corrosion resistance
Disadvantages:
Applicable only to stainless steel, not suitable for aluminum
May cause slight surface damage affecting long-term durability
Conclusion
Surface treatment plays a crucial role in enhancing the aesthetics and functionality of perforated metal panels, especially in terms of corrosion and pollution resistance. Selecting the right surface treatment method based on specific environmental conditions and functional requirements can significantly improve the lifespan and performance of the perforated panels. Whether for building facades, interior decoration, or industrial applications, the right surface treatment ensures optimal performance of perforated metal panels.
By understanding the different surface treatment methods, users can choose the most suitable perforated panels according to their actual needs, ensuring the best results in terms of aesthetics, functionality, and durability.