Applications and Characteristics of Perforated Sheets
Source:www.cn-psp.cnAuthor:河北森驰公司 Last updated:2025-03-17 14:40:58 Browse:
What Are Perforated Sheets?
Perforated sheets are materials manufactured using CNC punching technology, which creates various hole shapes on metal or non-metal sheets. Common materials include iron, aluminum, stainless steel, copper, nickel, fiberglass, and plastic. Due to their unique properties, perforated sheets are widely used in industries such as construction, machinery manufacturing, noise reduction, and filtration systems.
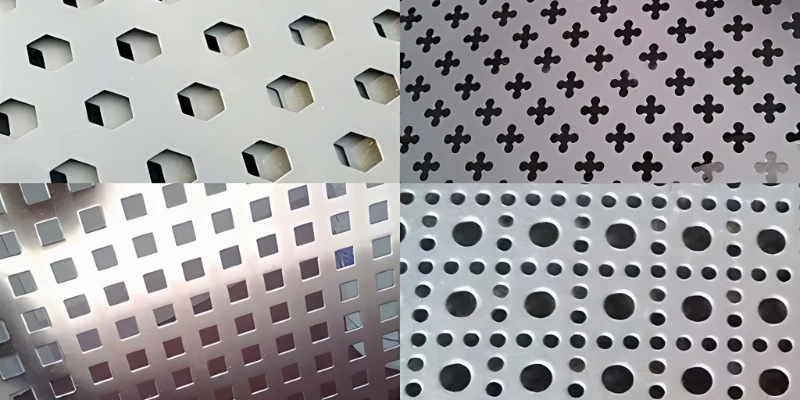
Key Characteristics of Perforated Sheets
1. Smooth and Flat Surface
During the manufacturing process, perforated sheets are precisely processed to ensure a smooth, burr-free surface. This not only enhances the aesthetics of the material but also minimizes safety hazards caused by rough edges. A smooth surface is beneficial for further processing such as painting, electroplating, and welding, making perforated sheets ideal for high-standard industrial applications.
2. Flexible Design and Aesthetic Appeal
Perforated sheets can be customized with various hole shapes, including round, oval, square, hexagonal, fish-scale, and other artistic patterns. This flexibility makes them popular in architectural decoration, interior design, and artistic installations. Additionally, perforated sheets can be treated with powder coating, anodizing, or galvanizing to achieve different colors and surface finishes, meeting modern architectural aesthetics.
3. High Strength and Durability
Unlike welded or woven mesh materials, perforated sheets are made from a single solid sheet, eliminating weak points at joints and ensuring superior structural strength and durability. This makes them ideal for use in harsh environments, such as protective covers for industrial machinery or building facades exposed to the elements.
4. High Open Area for Ventilation and Light Transmission
Perforated sheets can have an open area of up to 70% or more, allowing excellent airflow, filtration, and light transmission while maintaining structural integrity. A high open area improves ventilation efficiency, making perforated sheets suitable for ventilation systems, noise barriers, and filtration applications. This feature also helps keep the material lightweight while ensuring optimal performance in various environments.
5. Precision Hole Sizes
Advanced CNC technology ensures precise hole spacing and dimensions in perforated sheets, with tolerances as low as ±0.1mm. This level of accuracy is crucial for applications requiring precise hole patterns and spacing, such as electronic devices, screens, and mechanical components, where precision plays a key role in product performance and quality.
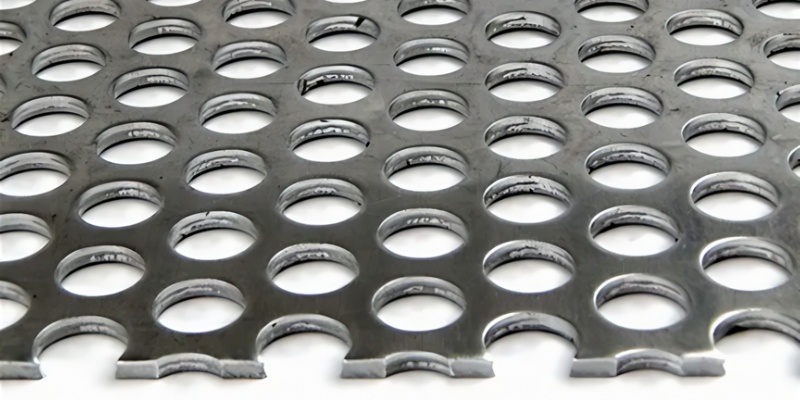
6. Excellent Corrosion Resistance
Stainless steel perforated sheets offer exceptional corrosion resistance, withstanding exposure to chemicals, moisture, and harsh weather conditions. For iron and aluminum sheets, surface treatments such as powder coating or fluorocarbon coating provide additional protection against rust and corrosion. This makes perforated sheets ideal for use in environments where durability and resistance to rust are critical, such as outdoor building materials and industrial applications.
7. Easy Secondary Processing
Perforated sheets are highly versatile when it comes to secondary processing. They can be easily cut, bent, laser-cut, polished, coated, and rolled to meet specific requirements. This flexibility allows for customized perforated sheets tailored to different applications, whether for creating unique shapes or adjusting hole patterns and spacing. For instance, perforated sheets can be fabricated into irregular shapes or adapted to specific design needs.
Main Applications of Perforated Sheets
1. Architectural Decoration and Facades
As decorative materials for building facades, perforated sheets enhance both the aesthetic appeal and ventilation of structures. They are widely used in curtain walls, ceilings, stair railings, and balcony enclosures, offering a modern and stylish design element while improving air circulation.
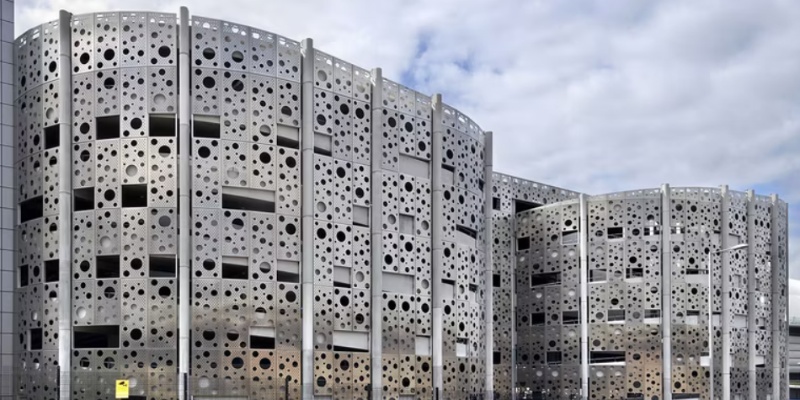
2. Noise Reduction and Acoustic Insulation
Thanks to their high open area and excellent sound-diffusing properties, perforated sheets are commonly used for soundproof walls, acoustic panels, and noise barriers. In transportation hubs, industrial workshops, and office spaces, perforated sheets help reduce noise pollution and create a more comfortable environment.
3. Filtration and Ventilation Systems
Perforated sheets are widely used in air and liquid filtration systems, as well as ventilation applications. They are essential components in HVAC (Heating, Ventilation, and Air Conditioning) systems, dust-proof screens, oil-gas separators, and water filtration units. Their high permeability and corrosion resistance make them indispensable in environmental protection and industrial filtration processes.
4. Protective Covers for Machinery
In the machinery manufacturing industry, perforated sheets are used as protective covers, shields, and grilles. They effectively safeguard machinery components while allowing proper ventilation and heat dissipation, thereby extending the lifespan of industrial equipment.

5. Agriculture and Food Processing
Perforated sheets play an important role in agriculture as grain sieving screens, livestock enclosures, and greenhouse shading systems. In the food processing industry, they are used to manufacture food-grade drying racks, ventilation trays, and filtration screens, contributing to increased production efficiency and improved product quality.
6. Transportation and Safety Barriers
In the transportation sector, perforated sheets are used for highway guardrails, metro station ventilation systems, and security fences. Their lightweight nature, high strength, and weather resistance make them an ideal material for protective and safety applications.
Conclusion
Due to their multifunctionality, high strength, corrosion resistance, and flexible design options, perforated sheets have become an essential material across multiple industries. Whether in architecture, machinery, acoustics, or filtration systems, perforated sheets provide effective solutions for various applications. With ongoing advancements in manufacturing technology, the application scope of perforated sheets continues to expand, particularly in smart buildings, green energy, and high-end manufacturing sectors, where demand is expected to grow significantly.