Common Secondary Processing Methods for Perforated Metal Sheet
Source:www.cn-psp.cnAuthor:河北森驰公司 Last updated:2025-05-27 11:15:30 Browse:
Perforated Metal Sheet is widely used in construction, manufacturing, environmental protection, and transportation due to its excellent performance in ventilation, lighting, noise reduction, and aesthetics. To meet different application needs, perforated metal sheets often undergo various secondary processing treatments after production. These processes ensure the sheets can be used directly after delivery, eliminating the need for customers to modify them manually.
Below are the most common secondary processing methods for Perforated Metal Sheet and their characteristics:
1. Bending
Through bending, flat perforated sheets are shaped at specific angles to fit structural requirements.
This process not only enhances the strength and flatness of the sheet but also makes it suitable for applications such as frames, brackets, railings, and decorative components.
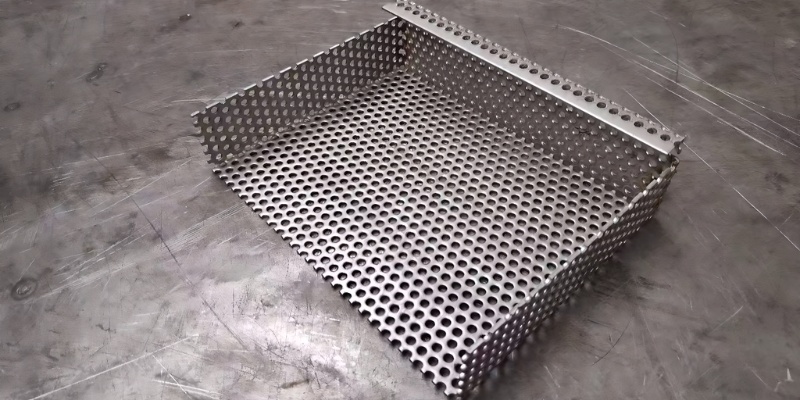
2. Laser Cutting
Laser cutting allows for precise and customized shaping of Perforated Metal Sheet, accommodating intricate and irregular designs.
It is particularly ideal for curtain walls, partitions, decorative panels, and mechanical parts requiring detailed patterns.
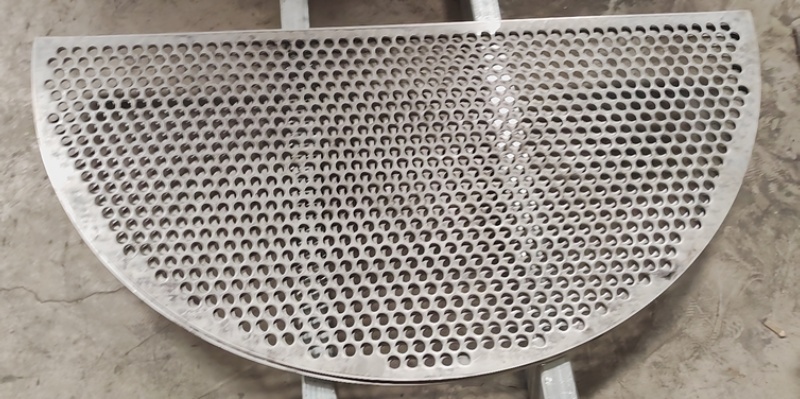
3. Rolling / Rounding
This technique forms Perforated Metal Sheets into arc or cylindrical shapes, making them easier to transport and install while meeting special structural design needs.
Common applications include building façades, pipe cladding, acoustic barriers, and artistic decoration.
4. Surface Spraying
To improve weather resistance and visual appeal, surface spraying is often applied.
Typical methods include powder coating, which is environmentally friendly and corrosion-resistant, suitable for outdoor installations; and fluorocarbon spraying, known for its superior UV resistance and durability under harsh conditions.
5. Welding & Assembly
Welding is used to join multiple sheets or combine sheets with other metal components, forming more complex structures.
Spot welding suits lightweight structures, while TIG welding (argon arc welding) is ideal for precision assemblies—frequently used in railings, sound barriers, metal decor, and machine enclosures.
6. Custom Perforation Patterns
In addition to standard hole shapes, Perforated Metal Sheets can be customized with unique designs to meet specific aesthetic and functional demands.
Popular custom options include decorative motifs and concentric holes, applicable in decorative walls, speaker panels, filters, and ventilation systems.
7. Surface Finishing
To enhance corrosion resistance and extend lifespan, various finishing techniques are applied.
Galvanizing is common for steel perforated sheets to prevent rust.
Anodizing enhances durability and appearance of aluminum sheets.
Brushed polishing gives stainless steel a refined and smooth surface finish.
Through these versatile secondary processing techniques, Perforated Metal Sheet products gain enhanced performance and adaptability, fulfilling the diverse demands of construction, manufacturing, transportation, and environmental industries.
When selecting processing services, it's recommended to collaborate with experienced manufacturers to ensure quality and precise customization.