Why Are More Perforated Steel Sheets Adopting Electrostatic Powder Coating?
Source:www.cn-psp.cnAuthor:河北森驰公司 Last updated:2025-06-11 18:21:09 Browse:
In the metal fabrication industry, perforated steel sheets are widely used in applications ranging from architectural facades and industrial filtration to mechanical protection systems. Their excellent ventilation, light transmission, and aesthetic appeal make them a popular choice. However, because they are prone to oxidation and rust in harsh environments, surface treatment is essential to enhance their durability and performance.
With technological advancement and increasingly stringent environmental regulations, traditional painting methods have gradually been replaced by a more efficient and sustainable alternative—electrostatic powder coating. This modern surface treatment process is rapidly becoming the industry standard for perforated steel sheets.
Limitations of Traditional Painting
In the past, spray painting was the dominant surface treatment for perforated steel sheets. It improved corrosion resistance and offered a wide variety of color options. Despite these benefits, the process had several major drawbacks:
Severe environmental pollution: Spray painting releases large quantities of volatile organic compounds (VOCs), which harm air quality and pose health risks to workers.
Weak adhesion: Paint coatings have limited bonding strength and are prone to peeling or bubbling over time.
Low efficiency: The painting process is time-consuming, requiring multiple coats and long drying periods, which increases production time and costs.
Poor weather resistance: Traditional paints tend to degrade under UV radiation, high heat, or cold conditions, shortening the lifespan of the coating.
These challenges have driven the search for better, more sustainable surface finishing solutions.
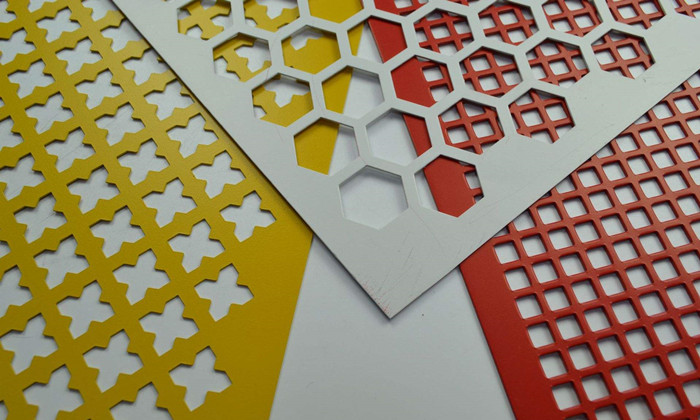
Advantages of Electrostatic Powder Coating
Electrostatic powder coating uses electrostatic charges to apply powder-based coatings evenly across the metal surface. The coated parts are then cured in a high-temperature oven, forming a strong, uniform, and durable finish. Compared to conventional paint, this method offers a range of compelling advantages:
1. Stronger adhesion and longer-lasting finish
Thanks to electrostatic attraction, the powder tightly bonds to the perforated steel surface. Once cured, the coating is dense and uniform, with an adhesion strength more than five times higher than traditional paint. This significantly improves resistance to impact and abrasion.
2. Outstanding weather resistance
Powder-coated surfaces offer superior protection against UV rays, high temperatures, low temperatures, and chemical corrosion. This makes electrostatic powder coating ideal for both indoor and outdoor environments, including humid and coastal areas.
3. Eco-friendly and sustainable
Powder coating is free of solvents and VOCs, making it far more environmentally friendly than spray painting. Excess powder can also be reclaimed and reused, reducing material waste and helping manufacturers meet green production standards.
4. High efficiency and lower cost
Unlike paint, which requires multiple coats and drying time, powder coating delivers optimal thickness in a single application. It cures faster and reduces production time, which cuts labor and energy costs significantly.
5. Rich color options and customization
Powder materials—including epoxy, polyester, and acrylic powders—can be blended to match any color from standard RAL charts. This makes it easy to achieve customized aesthetic results for various architectural and decorative uses.
Expanding Applications Across Industries
As the technology matures, electrostatic powder coating is being used in a growing range of applications for perforated steel sheets. These include building facades, partitions, mechanical equipment casings, ventilation covers, and electrical panel enclosures. Its ability to enhance both the visual and functional quality of metal products has made it a preferred choice among engineers, architects, and manufacturers alike.
Conclusion
As stricter environmental laws come into effect and customer demands for high-quality finishes increase, electrostatic powder coating is replacing spray painting as the go-to surface treatment for perforated steel sheets. This process not only enhances durability and appearance but also supports sustainable manufacturing goals. Looking ahead, with continued innovation in powder materials and coating equipment, powder coating is set to play an even greater role in the future of metal surface treatment.