How to Extend the Service Life of Iron Perforated Plates
Source:www.cn-psp.cnAuthor:河北森驰公司 Last updated:2025-03-03 14:59:55 Browse:
Iron perforated plates are widely used in construction, decoration, and industrial fields due to their high strength, corrosion resistance, and aesthetic appeal. However, to ensure these products maintain their performance and appearance over time, it is essential to take measures to extend their service life. Below, we explore various aspects of how to achieve this.
Selection of High-Quality Raw Materials
Material Determines Longevity
The service life of iron perforated plates is closely related to the quality of the raw materials used. High-quality low-carbon steel, stainless steel, or other alloy materials offer better strength and corrosion resistance, significantly extending the product's lifespan.
Control of Chemical Composition
During production, strict control over the chemical composition of the raw materials (e.g., proportions of carbon, silicon, and manganese) can enhance the product's tensile strength and corrosion resistance.
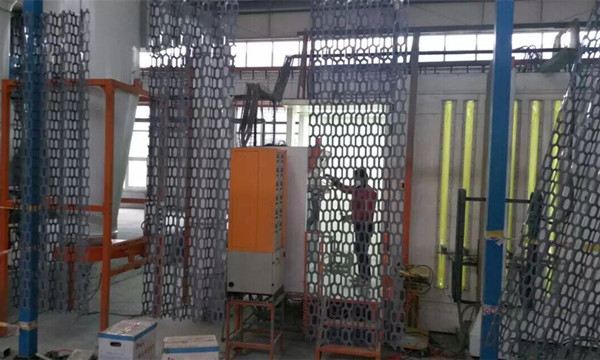
Surface Treatment Techniques
Hot-Dip Galvanizing
Hot-dip galvanizing is a common surface treatment process that applies a dense zinc layer to the iron plate, effectively preventing oxidation and corrosion. This method is ideal for outdoor applications of iron perforated plates.
Electroplating
Electroplating involves applying a thin zinc layer to the iron plate, providing good rust prevention. Compared to hot-dip galvanizing, electroplating is more cost-effective and suitable for scenarios with lower corrosion resistance requirements.
Dacromet (Thermosetting Coatings)
Dacromet is an eco-friendly surface treatment technology that forms a high molecular polymer coating through high-temperature curing. This process not only offers excellent corrosion protection but also enhances the product's visual appeal.
Phosphating
Phosphating creates a phosphate film on the iron plate, improving its corrosion resistance while providing better adhesion for subsequent coatings.
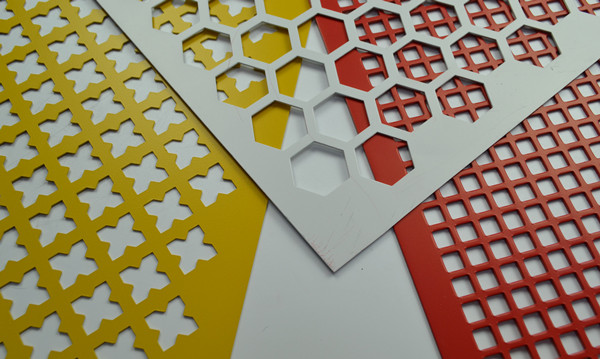
Design and Manufacturing Processes
Rational Structural Design
When designing iron perforated plates, it is crucial to avoid designs that concentrate stress. For example, adding support structures or optimizing hole distribution can help disperse stress and reduce the risk of fatigue-related damage.
Precision Punching Process
The precision of the punching process directly affects the product's strength and appearance. Using advanced CNC punching machines ensures uniform and consistent hole shapes, thereby improving overall product quality.
Non-Destructive Testing
After manufacturing, non-destructive testing methods such as ultrasonic testing and magnetic particle testing can detect minor defects (e.g., cracks or pores) in the product, helping to prevent early failures caused by quality issues.
Installation and Maintenance
1.Proper Installation Methods
Foundation Preparation: Before installing iron perforated plates, ensure the base surface is flat, dry, and properly treated for moisture protection.
Fixation Methods: Choose an appropriate fixation method (e.g., welding or bolt connections) based on the application to avoid loosening or deformation caused by improper installation.
2.Regular Inspection and Maintenance
Cleaning Dirt: Periodically clean dust, oil stains, or other residues from the surface of the iron perforated plates using soft brushes or high-pressure water guns.
Checking Corrosion: For products exposed to damp or corrosive environments, regularly inspect the surface coating for damage and repair any defects promptly.
Lubricating Moving Parts: If the iron perforated plates are connected to moving components (e.g., access control systems), regularly lubricate the moving parts to reduce wear and tear.
3.Avoiding Extreme Environments
Avoid exposing iron perforated plates to prolonged high temperatures, humidity, or strong acids/bases.
For outdoor use, consider materials with better weather resistance (e.g., stainless steel or aluminum alloys).
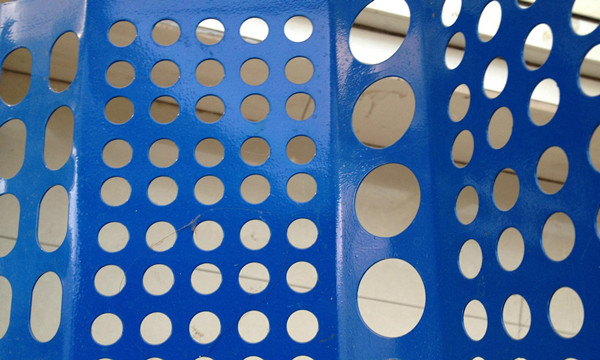
Comprehensive Recommendations
Choose Professional Manufacturers
When purchasing iron perforated plates, select manufacturers with extensive experience and a good reputation. These manufacturers typically use high-quality raw materials and advanced production processes to ensure product quality and longevity.
Select Materials Based on Application
Different usage scenarios have varying requirements for iron perforated plates:
Outdoor use: Recommend hot-dip galvanizing or stainless steel materials.
Indoor decoration: Ordinary low-carbon steel can be used, but proper surface protection is necessary.
Focus on Post-Maintenance
The service life of iron perforated plates depends not only on product quality but also on post-maintenance efforts. Regular inspections and maintenance can significantly slow down product aging.
Extending the service life of iron perforated plates requires attention to multiple factors, including raw material selection, surface treatment, design manufacturing, and installation maintenance. By using high-quality materials, advanced surface treatment techniques, optimized design processes, and strengthening post-maintenance management, you can significantly improve the durability and aesthetics of the product. I hope this information provides valuable insights for you!