Causes of Larger Burrs in Perforated Plates
Source:www.cn-psp.cnAuthor:河北森驰公司 Last updated:2025-04-09 14:08:10 Browse:
Perforated plates inevitably produce some burrs during the manufacturing process. Typically, if you touch the back of the perforated plate and the burrs are not too sharp or noticeable, they are generally within a reasonable range. However, if the burrs exceed this range, the perforated plate is considered a defective product. Below, we will briefly analyze the common causes of larger burrs in perforated plates.
1. Punch Pin Issues
Perforated plates are produced by continuous punching on CNC punching machines using alloy punch pins. The sharpness of the punch pin directly affects the size of the burrs on the back of the perforated plate. The dulling of the punch pin is one of the primary causes of larger burrs.
2. Punch Head Failures
The punch head is used to fix the punch pin. If the punch head is severely worn, it can cause improper installation of the punch pin, which in turn affects the burrs on the perforated plate. This issue requires timely inspection and repair during production.
3. Excessive Bottom Die Clearance
During the punching process, if the clearance between the bottom die and the punch pin is too large, it will result in larger burrs on the perforated plate. When the clearance is too wide, the material is not cut cleanly during punching, leading to bigger burrs.
4. Environmental Factors
In addition to production-related issues, burrs may also form during actual use due to environmental factors. For example, if a perforated plate is exposed to high acidity or alkalinity, it may undergo chemical reactions or come into contact with metal debris and liquids, which can lead to the formation of burrs.
5. Human Factors
During use, perforated plates may also develop burrs due to improper handling. For example, manual scraping or external impacts can cause burrs to form. Therefore, it is essential to handle perforated plates with care, regularly inspect them, and perform necessary maintenance and protection.
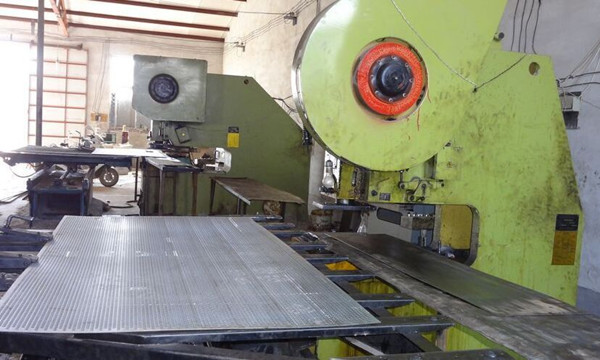
Solutions
To address the issue of excessive burrs on perforated plates, here are some effective solutions:
1. Enhance Operator Training
When the punch pin has worn to a certain extent, it should be repaired promptly to prevent the formation of excessive burrs. Operators should be well-trained and regularly check the equipment to ensure that the punch pin remains in good condition.
2. Regular Mold Inspections
Regularly inspect the molds, especially when the punch pin or mold is severely worn. In such cases, repairs or replacements should be made to ensure consistent production quality. This can effectively prevent large burrs caused by mold damage.
3. Optimize Production Processes
During production, adjusting the pressure and speed of the punching machine can help reduce burr formation. Additionally, using higher-quality punch pins and bottom dies can also help reduce the occurrence of burrs.
By implementing these optimization measures, not only can the quality of the perforated plates be improved, but burr problems can also be effectively reduced, thereby extending the product's lifespan. Strengthening management and maintenance during both production and use can significantly enhance the performance and effectiveness of the perforated plates.