How to Extend the Service Life of Aluminum Perforated Panels? – A Comprehensive Guide
Source:www.cn-psp.cnAuthor:河北森驰公司 Last updated:2025-03-17 15:08:02 Browse:
Aluminum perforated panels are widely used in architectural decoration, machinery manufacturing, ventilation systems, and more due to their lightweight, high strength, and aesthetic appeal. However, to maximize their lifespan and maintain their performance over time, the following key measures are essential.
1. Optimize Manufacturing Processes for Enhanced Durability
High-quality manufacturing processes are the foundation of durable aluminum perforated panels. Advanced punching technology and precision equipment should be used to ensure uniform perforations and smooth edges, reducing stress concentration and the risk of early damage. Additionally, selecting high-purity and uniform aluminum alloy materials can significantly improve the durability of the panels.
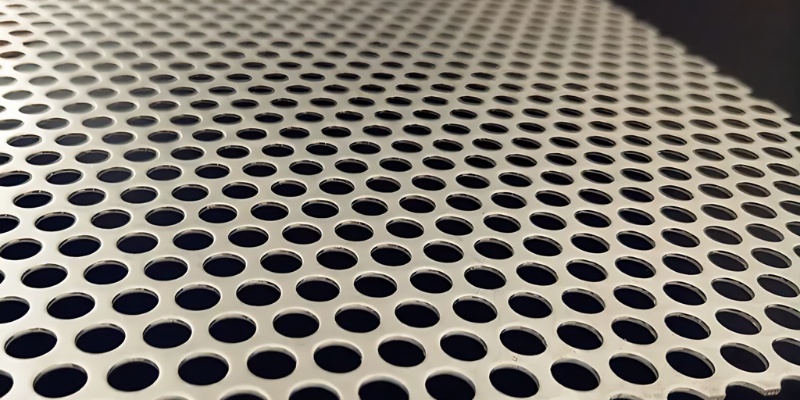
2. Proper Usage to Prevent Excessive Wear
The service environment directly impacts the lifespan of aluminum perforated panels. When installing and using these panels, it is crucial to avoid highly corrosive environments (such as areas with severe acidic or alkaline gases) and excessive load-bearing conditions to prevent oxidation, deformation, or breakage. Proper installation methods should also be followed to prevent uneven stress that could lead to cracks or distortion.
3. Regular Cleaning and Maintenance to Prevent Corrosion
Dust, grease, and other contaminants can accelerate corrosion, making regular cleaning essential. It is recommended to use a neutral detergent and a soft cloth for wiping while avoiding strong acidic or alkaline cleaners. In humid or salt-laden environments, cleaning should be performed more frequently to reduce the impact of corrosive substances on the aluminum surface.
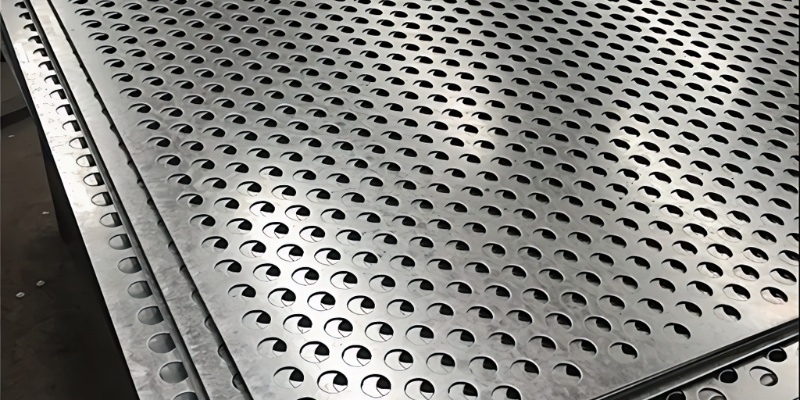
4. Surface Treatments for Enhanced Protection
To further improve the corrosion resistance of aluminum perforated panels, protective coatings can be applied, such as:
Anodizing: Forms an oxide layer on the aluminum surface to enhance corrosion and wear resistance.
Powder Coating or Fluorocarbon Coating: Increases resistance to UV exposure and minimizes damage caused by environmental factors.
Anti-Rust Coating: In harsh environments, applying specialized protective coatings can effectively extend the lifespan of perforated panels.
5. Regular Inspections and Timely Replacement of Damaged Panels
It is crucial to conduct regular inspections, especially for panels exposed to high loads or harsh environments. If cracks, deformations, or severe wear are detected, they should be replaced promptly to prevent safety hazards. Additionally, when storing unused perforated panels, ensure they are kept dry and protected from moisture and mechanical damage.
Conclusion
By optimizing manufacturing processes, using panels properly, performing regular maintenance, applying protective coatings, and conducting timely inspections and replacements, the service life of aluminum perforated panels can be significantly extended. These measures not only maintain the panels’ aesthetic and functional qualities but also enhance their long-term value, providing reliable solutions across various industries.