What Are the Differences Between Stainless Steel Perforated Panels and Aluminum Alloy Perforated Panels?
Source:www.cn-psp.cnAuthor:河北森驰公司 Last updated:2025-03-09 15:14:38 Browse:
In industries such as construction decoration, noise reduction, and various other fields, metal perforated panels are widely used due to their aesthetic appeal, durability, and versatile functionality. Among them, stainless steel perforated panels and aluminum alloy perforated panels are two of the most common types. So, what are the differences between them? Which material is more suitable for your needs? This article will provide a detailed comparison based on material properties, corrosion resistance, weight, price, and processing performance to help you make an informed choice.
1. Comparison of Material and Properties
Stainless Steel Perforated Panels: Mainly made of stainless steel materials such as 201, 304, and 316, these panels offer excellent strength and corrosion resistance, making them ideal for high-demand industrial or outdoor environments.
Aluminum Alloy Perforated Panels: Made from aluminum alloys such as 1060, 3003, 5052, and 5083, these panels are lightweight and highly resistant to oxidation, making them suitable for applications requiring aesthetics and durability but not high load-bearing capacity.
Summary: Stainless steel perforated panels are more robust and durable, while aluminum alloy perforated panels are lighter and easier to process.
2. Comparison of Corrosion Resistance
Stainless Steel Perforated Panels: Stainless steel 304 and 316 offer excellent corrosion resistance, enabling long-term use in humid, acidic, and alkaline environments. Particularly, 316 stainless steel performs exceptionally well in marine environments and chemical plants.
Aluminum Alloy Perforated Panels: Aluminum naturally forms a dense oxide layer when exposed to air, enhancing its corrosion resistance. However, in highly acidic or alkaline environments, aluminum alloys are less corrosion-resistant compared to stainless steel.
Summary: For harsh environments (such as humidity, acidic, and alkaline conditions), stainless steel perforated panels are recommended. For general indoor decoration or dry environments, aluminum alloy perforated panels are also a good choice.
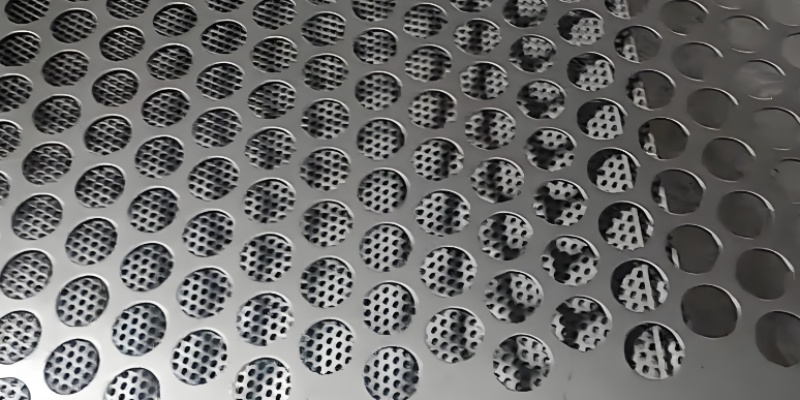
3. Comparison of Weight
Stainless Steel: With a density of approximately 7.93 g/cm³, stainless steel is relatively heavy and advantageous for structures requiring high-strength support.
Aluminum Alloy: With a density of about 2.7 g/cm³, which is roughly one-third that of stainless steel, aluminum alloy perforated panels are more suitable for weight-sensitive applications such as ceilings and exterior wall decorations.
Summary: Aluminum alloy perforated panels are lighter, reducing installation and transportation costs, whereas stainless steel perforated panels are stronger and more suitable for high-strength applications.
4. Comparison of Price
Stainless Steel Perforated Panels: These are more expensive, especially the 316 variant, due to its superior corrosion resistance and strength.
Aluminum Alloy Perforated Panels: These are more cost-effective, and since aluminum is easily recyclable, the overall economic efficiency is higher.
Summary: If budget constraints are a concern and high corrosion resistance is not required, aluminum alloy perforated panels are a suitable option. If durability and strength are the priority, stainless steel perforated panels are the better choice.
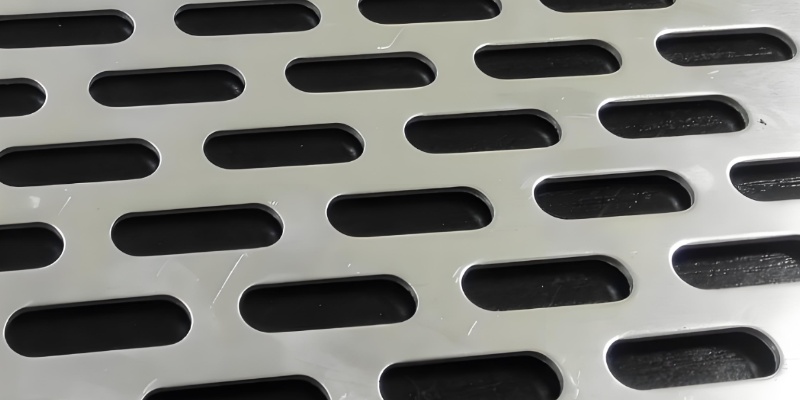
5. Comparison of Processing Performance
Stainless Steel Perforated Panels: High hardness makes punching and bending more challenging, requiring advanced processing equipment and technical expertise.
Aluminum Alloy Perforated Panels: Softer material makes them easier to process and customize into various complex patterns and shapes, making them more popular in architectural decoration.
Summary: Aluminum alloy perforated panels are easier to process and suitable for complex designs, while stainless steel perforated panels are harder and better suited for high-strength applications.
6.Comparison of Main Application Scenarios

7. How to Choose the Right Perforated Panel?
Choose stainless steel perforated panels if your project requires:
High strength and impact resistance (e.g., safety protection, industrial applications)
Excellent corrosion resistance (e.g., chemical plants, food processing plants)
Long-term outdoor use (e.g., coastal areas, regions with acid rain)
Choose aluminum alloy perforated panels if your project requires:
Lightweight and easy installation (e.g., ceilings, curtain wall decoration)
Good plasticity (e.g., customized shapes)
Cost-effectiveness (e.g., large-area decorations)
Conclusion
Both stainless steel and aluminum alloy perforated panels have their advantages, and the choice depends on your project requirements. If you need higher strength, corrosion resistance, and durability, stainless steel perforated panels are the better choice. If you require a lighter, more easily processed, and cost-effective material, aluminum alloy perforated panels are a great option.
If you need custom metal perforated panels with various specifications, hole patterns, and thicknesses, feel free to contact us. As a professional manufacturer of metal perforated panels, we provide high-quality customization services tailored to your needs!