Will Galvanized Perforated Sheets Rust?
Source:www.cn-psp.cnAuthor:河北森驰公司 Last updated:2025-04-17 10:15:55 Browse:
In modern architectural decoration, industrial partitions, and curtain wall design, galvanized perforated sheets have become the industry’s top choice for their aesthetics, versatility, and excellent corrosion resistance. However, many clients wonder: will galvanized perforated sheets rust? This article delves into the anti‑rust principles of galvanized perforated sheets from three perspectives—manufacturing process, usage environment, and maintenance—and offers practical tips to extend their service life.
1. Manufacturing Process: Direct Perforation vs. Post‑Galvanizing
Direct Perforation (Galvanize → Punch)
Advantages: Lower cost, higher production efficiency.
Disadvantages: Punching destroys the zinc layer at hole edges, creating “weak rings” that easily become rust initiation points.
Post‑Galvanizing (Punch → Acid Clean → Hot‑Dip Galvanize)
Advantages: Zinc layer uniformly covers hole edges, forming a complete protective film that greatly enhances rust protection and corrosion resistance.
Disadvantages: More complex process and slightly higher cost, but offers better value—ideal for projects with high service‑life requirements.
2. Usage Environment: Regional Differences
Coastal & High‑Humidity Areas
Sea breeze contains salt and moisture that accelerate zinc oxidation and flaking, potentially leading to localized rust spots.
Recommendation: Choose post‑galvanized sheets with a high zinc coating (≥ 80 μm) and regularly wash off salt deposits.
Inland & Dry Regions
Low ambient humidity reduces corrosion stress on galvanized perforated sheets.
Recommendation: A standard zinc coating (≥ 50 μm) can achieve an outdoor lifespan of 5–10 years.
3. Maintenance: Regular Inspections Are Essential
Cleaning: Wipe with a neutral detergent every six months to remove dust and grime, preventing acidic or alkaline damage to the zinc layer.
Touch‑Up: If you spot zinc layer peeling at hole edges or bends, apply a zinc powder or zinc‑silicon touch‑up spray.
Avoid Mechanical Damage: Handle with care during transport and installation to prevent dents or scratches that break the zinc coating.
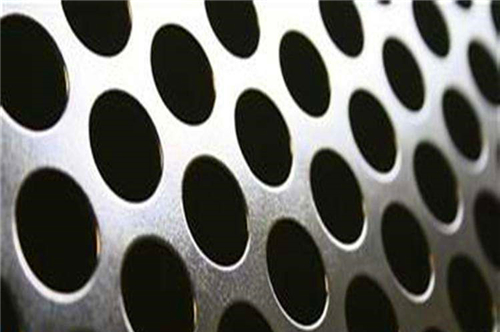
II. How to Extend the Service Life of Galvanized Perforated Sheets
Select the Right Process
Recommend the full “Punch → Acid Clean → Hot‑Dip Galvanize” workflow to ensure uniform zinc coverage on hole edges and folds.
Ensure Proper Drainage Design
Install sheets with a slight tilt to avoid water pooling, reducing prolonged zinc layer immersion.
Apply Additional Protective Coatings
For extreme conditions (e.g., chemical plants, seaside buildings), consider a secondary powder‑coating or plastic coating over the galvanized layer for double protection and enhanced durability.
Perform Annual Maintenance Inspections
Inspect surfaces yearly, promptly repair damaged areas, and clean contaminants to maintain an intact zinc barrier.
Summary
Galvanized perforated sheets inherently offer excellent rust protection and corrosion resistance, but actual rusting depends on manufacturing process, environment, and maintenance.
Employing a “Punch → Post‑Galvanize” process combined with regular upkeep can deliver over 10 years of service life in most settings.
In coastal or highly corrosive environments, opt for thicker zinc layers and secondary protective coatings, and conduct frequent cleaning and repairs to keep the protective film intact.
For more specifications, process details, or custom solutions, please feel free to contact us!